HIGH-PERFORMANCE COMPOSITE REPAIR SOLUTION FOR PIPE REINFORCEMENT
DEFECT TYPE | internal corrosion defect + 3 holes |
DETAILS | 10” spool – water line – max. op. temp. 40°C – op. pressure 9 bars – application temp. 130°C |
LOCATION | QATAR |
3X PRODUCT | REINFORCEKiT® 4D |
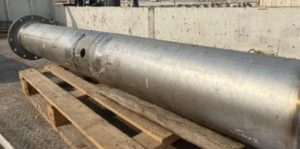
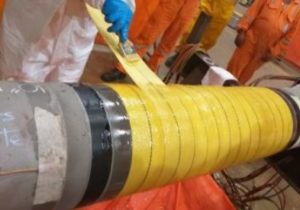
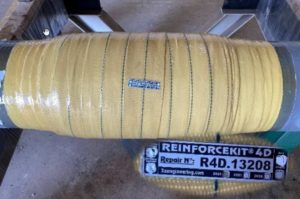
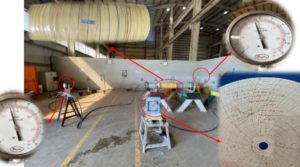
OVERVIEW
The objective of the test, performed, by 3X ENGINEERING (3X) local distributor PEC, was to reinforce 10” spool suffering from internal corrosion defect and 3 holes. This test was required by the client to qualify our R4D composite system before performing the physical wrapping on site.
SCOPE OF WORK
Before starting the test, the spool was inspected, climatic conditions were checked, surface preparation was performed using sand blasting machine and surface profile was evaluated. Heating element process was then performed by a third party to preheat the specific area to be repaired at 130°C during minimum of 4 hours for application and 10 hours for full curing.
The repair length was measured, surface cleaning using acetone and hygrometric tests were performed before composite wrapping.
The reinforcement was then performed as follows. These steps are the same ones for the 3 holes. For internal corrosion defect, no metallic plate was necessary (step 1 not applicable).
1. Metallic plates (previously prepared to ensure a good bonding with the substrate) were installed using F3XS1 filler on the defected areas and fastened with ratchet belts for good tightening. One metallic plate 100x95mm dimensions for 50mm hole and 2 metallic plates 31x24mm dimensions for 8mm pinholes. This step did not require any specific curing time.
2. Impregnation of the surface with 3X specific resin to ensure good wetting and impregnation of the Kevlar® tape.
3. Kevlar® tape impregnated with 3X specific resin and wrapped around the pipe. According to ISO 24.817 and 3X repair calculations, 42 layers of R4D were determined to reinforce defected area for a total repair length of 703mm.
4. Finalization of the repair with reference plate positioning for traceability purpose.
Twelve hours of curing load between 107°C and 135°C were necessary for the complete polymerisation of the composite wrapping system to provide full mechanical characteristics before hydrotest.
RESULTS
REINFORCEKiT® 4D composite system efficiently passed the hydrotest at 9 bars for 2h and 50mn. No leak was observed and concluded the successful mockup test. This mockup project was a great challenge due to the application at 130°C and the several internal and hole defects. DNV GL inspection report certified our R4D composite system.