HIGH-PERFORMANCE COMPOSITE REPAIR SOLUTION FOR PIPE REINFORCEMENT
DEFECT TYPE | 2 dents in subsea environment |
DETAILS | 48” oil line – max. op. temp. 35°C – op. pressure 18.2 bars |
LOCATION | QATAR – Halul Island |
3X PRODUCT | REINFORCEKiT® 4D Subsea (R4D-S) |
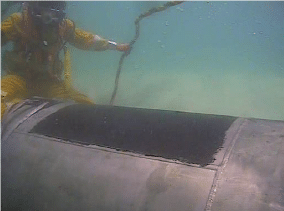
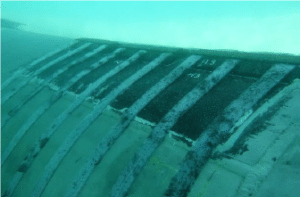

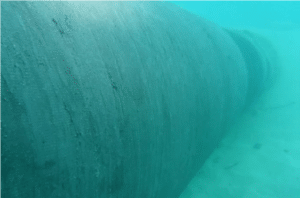
OVERVIEW
The objective of the repair, performed by 3X ENGINEERING (3X) and its local distributor PEC, was to reinforce a 48” subsea pipe damaged by 2 dents (between 7 and 10-meter depth).
SCOPE OF WORK
According to ISO 24.817 and 3X repair calculations, 32 layers of R4D-S have been determined to reinforce the damaged pipe section (dent No. 1 measured 840mmx445 and dent No. 2 measured 770mmx482mm).
Underwater, preliminary operations (pipeline excavation, concrete removing etc …) were performed prior to surface preparation by grit blasting to get a good surface profile (superior to 60µm).
The composite repair was then performed following 6 main stages (these steps are the same ones for the 2 dented defects):
1. Before primer application, ratchet belts were installed over the pipe near the defect to ensure the good composite plate installation and tightening (step 3).
2. P3X30 primer application right on the defect to ensure a good bonding of the composite plate (step 3).
3. F3XSS filler application on rigid composite plate. The plate was then given to the diver and positioned over the dent and fastened tightly with ratchet belts (previously installed – see step 1).
4. Another P3X30 primer layer was then applied on the whole surface of the repair to provide a good adhesion of the composite material with the surface before wrapping. No specific curing time was required.
5. Kevlar® tape impregnated with R3X1050S resin and wrapped around the pipe. The tape impregnation was performed using BOBIPREG® (3X specific machine allowing a quick and regular impregnation resin/fiber). Thirty-two layers were necessary to repair the defect (i.e. 16 passes of 50% overlap) for a total of 3m repair length.
6. Finalization of the repair with reference plate positioning for traceability purpose and validation of the repair using hardness measurements.
RESULTS
The subsea reinforcement was successfully repaired using REINFORCEKiT® 4D SUBSEA product. This project was a great challenge due to the large diameter of the line and the shallow water position of the defects. Meantime, all the teams involved in the project faced with this international COVID-19 pandemic, with all the constraints and difficulties associated for the manpower, the shipment of the material, the quarantine time…