HIGH-PERFORMANCE COMPOSITE REPAIR SOLUTION FOR PIPE REINFORCEMENT
DEFECT TYPE | 5 defects of internal corrosion |
DETAILS | 8” pipe spools -gas line – max. op. temp. 40°C – op. pressure 81 bars |
LOCATION | QATAR, Ras Laffan treatment plant |
3X PRODUCT | REINFORCEKiT® 4D |
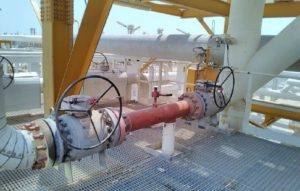
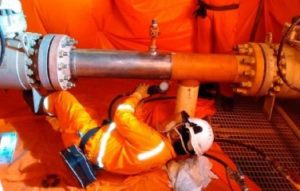
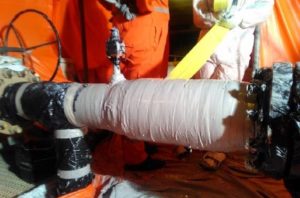
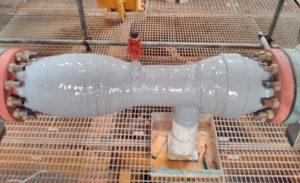
OVERVIEW
The objective of the repair, performed by 3X ENGINEERING (3X) local distributor PEC, was to reinforce two 8” pipe spools suffering from internal damages pipe spool A damaged by 3 defects + pipe spool B with 2 defects.
SCOPE OF WORK
The job was carried out on 2 different pipe spools (both with same details) using R4D. Below is firstly described the repair of pipe spool A damaged in 3 locations (3.8mm, 5mm and 7mm metal loss).
Before starting the repair, surface preparation was completed with Bristle Blaster pneumatic machine (ATEX approved) to get a good surface roughness and ensure the bonding between the pipe spool and the composite. Surface profile evaluation was performed to confirm the roughness was superior to 60µm. Hygrometric conditions were checked and the whole prepared surface was cleaned with acetone.
The composite wrapping reinforcement was then performed as follows. These steps are the same ones for the 2 defects near the flanges (to reinforce the middle area defected, no metallic plate was necessary).
1. Metallic plate (previously prepared to ensure a good bonding with the substrate) was installed using F3XS1 filler on the defected area and fastened with ratchet belts for good tightening.
2. Impregnation of the surface with R3XHT+ resin to ensure good wetting and impregnation of the Kevlar® tape.
3. Kevlar® tape impregnated with R3XHT+ resin and wrapped around the pipe. According to ISO 24.817 and 3X repair calculations, 86 layers of R4D have been determined to reinforce the 2 defects situated on the extremities of the pipe spool, near the flanges. Only 6 layers were needed to reinforce the middle area for a total repair length of 1433mm.
4. Finalization of the repair with reference plate positioning for traceability purpose and validation of the repair using hardness measurements.
Process repair was the same to reinforce the pipe spool B damaged by 2 internal defects: 86 layers for defect 1 near the flange (5.82mm metal loss) and 6 layers for defect 2 (7.9mm metal loss) for a total repair length of 1350mm.
RESULTS
This project was a great challenge due to the pipe spools geometry (i.e. defects near to the flange area) but has been successfully completed on time despite international COVID-19 pandemic and all the safety measures and constraints associated.