PROTECTIVE COMPOSITE SOLUTION FOR CORROSION UNDER PIPE SUPPORT
DEFECT TYPE | Pipe & supports protection |
DETAILS | 6” straight flowline – crude oil – design press. 110 bars |
LOCATION | QATAR |
3X PRODUCT | ROLLERKiT® |
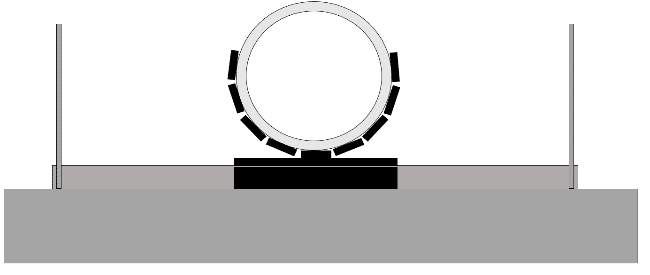
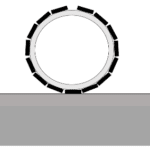
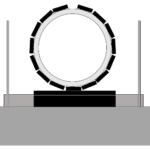
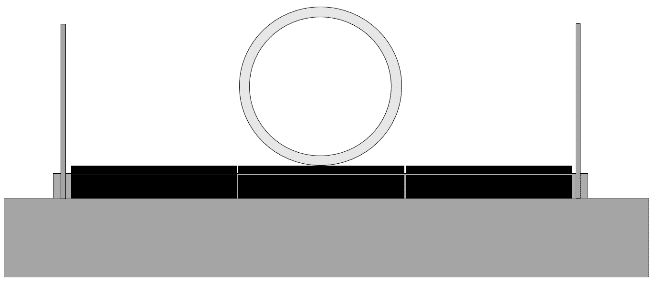
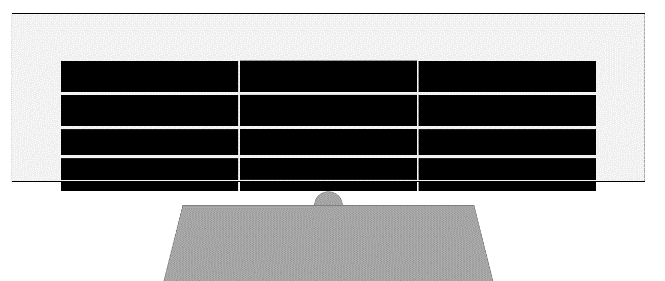
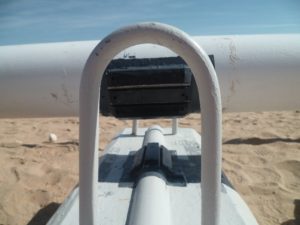
OVERVIEW
The client had some problems of deterioration between the pipe and its supports. The objective of the test required was to evaluate 3X solution to solve this problem. The test performed by 3X specialists, in collaboration with PEC (3X Distributor in Qatar), was to install our ROLLERKiT® (product specifically dedicated to protect the area between the pipe and the support) on the line in 5 different configurations to test the effectiveness and reliability of this solution.
SCOPE OF WORK
ROLLERKiT® can be installed both on pipe or on support without shutdown.
According to client’s requirements and after calculations, see below the 5 various configurations performed for the test.
* Location #1 9 pads were installed on the pipe + 3 pads on the support (both pipe and support were blasted)
* Location #2 15 pads were installed on the pipe to protect the whole outside surface of the pipe (pipe was blasted)
* Location #3 15 pads were installed on the pipe + 3 pads on the support (application without blasting).
* Location #4 6 pads were installed on the support (application without blasting).
* Location #5 3×9 pads were installed on the pipe (application without blasting).
The 5 repairs were performed following the same stages:
PIPE OR SUPPORT SURFACE PREPARATION (depending on the configuration and where the pads were applied) using sandblasting in order to get a surface roughness Rz > 60µm. Degreasing and cleaning using acetone to ensure that the prepared surface is completely free from residue.
ROLLERKiT® PREPARATION. Cutting of the necessary number of pads to be installed. Mixing and application of F3X8 filler on the pipe/support previously prepared and on the ROLLERKiT® (fiber glass side).
ROLLERKiT® APPLICATION. ROLLERKiT® was then fixed on the pipe/support. For the configurations with pads installed on the pipe, ratchets belts and air bubble system were used to control the positioning.
REPAIR FINALIZATION AND VALIDATION. When curing time was over, ratchet belts were removed and hardness measurements were performed to confirm the good polymerization of the filler.
RESULTS
The test was successfully managed by 3X specialists. ROLLERKiT® was installed in 5 various configurations as required by the client (with/without blasting, on pipe only, on support only, both on pipe and support).
More than 2 years and half after installation, Inspection was carried out and concluded the big success of the test and the efficiency of the ROLLERKiT®.
Conclusion was transmitted by the client:
ROLLERKiT® application on flowline support contact area found intact
No wear and tear observed on ROLLERKiT®
Flowline is protected at support contact point efficiently