HIGH-PERFORMANCE COMPOSITE REPAIR SOLUTION FOR PIPE REINFORCEMENT
DEFECT TYPE | Internal corrosion |
DETAILS | 44” ballast water line - max. operating temp. 25°C – design press. 6 barg |
LOCATION | Ain Sokhna, EGYPT |
3X PRODUCT | REINFORCEKiT 4D (R4D) |
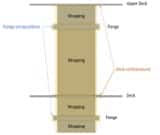
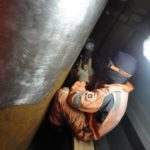
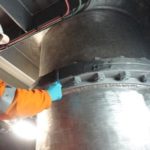
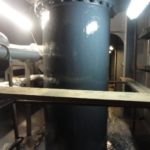
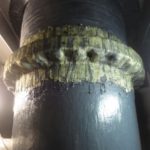

OVERVIEW
The objective was to reinforce a 44” ballast line and encapsulate 2 flanges of a vessel, damaged by internal corrosion (79% metal loss).
SCOPE OF WORK
After calculations and Finite Elements Analysis (FEA), 8 layers have been determined to perform the reinforcement.
In consultation with the client, we have decided to extend the length of the repair from 310mm to 4000mm to cover all the pipe (from under the flange, below the deck, to the upper deck). Prior to 3X intervention, coating was removed on the section to be repaired.
Surface preparation was then completed by 3X team, using Bristle Blaster machine, to get a good surface roughness (superior to 60µm) and ensure the bonding between the steel pipe and the composite. Climatic conditions have been checked and the surface has been cleaned and degreased with Acetone.
The composite repair has been performed following 6 main stages:
1/ F3XS1 filler application on flanges and deck weld.
2/ R3X5 resin application (1 layer) on the whole pipe surface to protect it from corrosion.
3/ Reinforcement process was then started on the deck weld using Kevlar® strips impregnated with R3X5 resin 70 strips were necessary to make 1 pass all around the pipe (i.e. 2 layers). This step was repeated 4 times to reach the 8 layers.
4/ F3XCOMB filler application to encapsulate the 2 flanges and reshape their profile to facilitate composite application.
5/ Same reinforcement process was completed on flanges using Kevlar® strips and R3X5 resin 87 strips applied for 1 pass (i.e. 2 layers). This step was repeated 4 times to reach the 8 layers.
6/ Wrapping process covering the total surface (i.e. straight part of the pipe and flanges) was finally completed using Kevlar® tape and R3X5 resin.
Last layer of R3X5 resin was applied on the whole repair and identification plate for traceability has been positioned on the pipe. Hardness measurements have been performed 3 days after job completion.
RESULTS
The 44” ballast line suffering from internal corrosion was successfully repaired using REINFORCEKiT® 4D. The total length of the repair was 4m. A special thanks to client team who helped us to work in the best conditions.