HIGH-PERFORMANCE COMPOSITE REPAIR SOLUTION FOR PIPE REINFORCEMENT
DEFECT TYPE | Internal corrosion pittings |
DETAILS | PIPES DETAILS: ¾ straight piping lines – oil – design temp. 74°C – design pressure 144 barg |
LOCATION | QATAR |
3X PRODUCT | REINFORCEKiT® 4D |
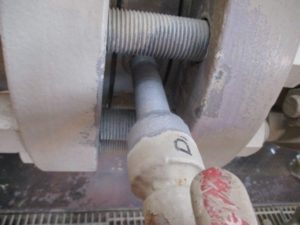
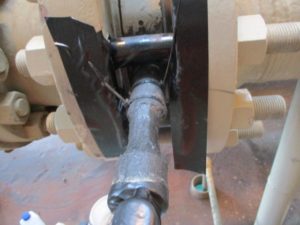
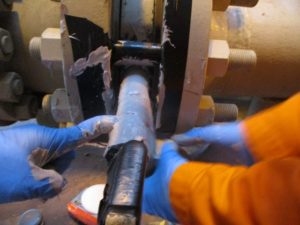
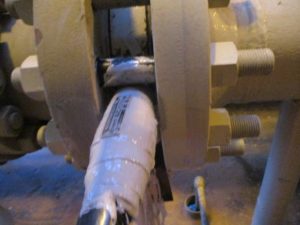
OVERVIEW
The objective of the repair, performed by 3X ENGINEERING (3X) local distributor POWER ENGINEERING CORPORATION (PEC), was to reinforce 2 areas suffering from internal corrosion pitting defects.
SCOPE OF WORK
Calculations using 3X software and according to ASME PCC-2 were performed to define the design of the repair. 3X and PEC advised to apply 14 layers of REINFORCEKiT® 4D to reinforce both piping lines suffering from internal corrosion defects (10mm defect length).
Before starting the composite reinforcements, surface preparation was completed with grit blasting to get a good surface roughness and ensure the bonding between the pipe and the composite.
Surface profile evaluation was performed to confirm the roughness was superior to 60µm. The surface was then cleaned using acetone and hygrometric conditions were checked before wrapping procedure (steps described below are the same for each reinforcement).
1. Metallic plate (previously sandblasted and bended to fit with the geometry of the damaged area) covered with 3X specific filler was applied on the defected area and fixed using fastened belts. Excess of filler was used to further smooth the edges of the plate. Climatic conditions were checked before moving on composite wrapping.
2. Wrapping process to reinforce the defected area (previously covered with epoxy resin to ensure good wetting and impregnation of the tape) was completed using Kevlar® tape (specific size tape for small pipe diameter) impregnated with 3X high-temperature resin a total of 14 layers was applied for 180mm repair length.
3. Last layer of epoxy resin was applied all over the repair and reference plate was installed on each repair for traceability purpose.
For each repair, samples of filler and resin were taken during application for quality control.
RESULTS
The 2 piping lines were successfully repaired using REINFORCEKiT® 4D. composite solution (repair lifetime: 2 years). This project was quite complicated due to the ¾ spools geometry and difficult accessibility to perform the repair but was completed on time as per the schedule required by the client. All the COVID-19 safety measures were correctly respected.