PROTECTIVE COMPOSITE SOLUTION FOR CORROSION UNDER PIPE SUPPORT
DEFECT TYPE | Corroded pipe supports |
DETAILS | PIPE DETAILS: 8” pipeline – oil – pressure: 12 bars - 14” pipeline – gas – pressure: 66 bars |
LOCATION | IVORY COAST |
3X PRODUCT | ROLLERKiT® with REINFORCEKiT 4D |
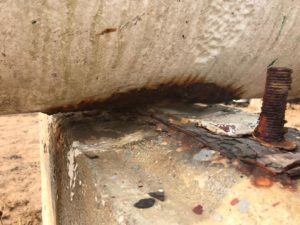
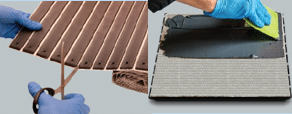
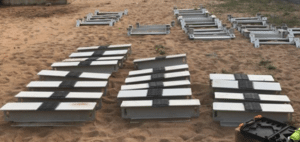
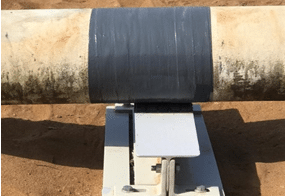
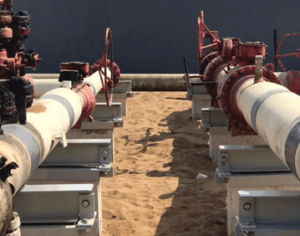
OVERVIEW
The client had some problems of corrosion between the pipe and its supports. The objective of the job, performed in February 2021 by local 3X ENGINEERING (3X) distributor PROMETRIC was to reinforce and protect the area between the pipe and the support a combination of ROLLERKiT® and R4D solutions was selected.
SCOPE OF WORK
As the corrosion was minor, 2 layers of R4D composite wrapping were proposed to restore pipe integrity and stop corrosion process. For this configuration, it was decided to apply ROLLERKiT® on the support for convenience.
The repairs were performed following the same stages:
1. PIPE SURFACE PREPARATION. Corroded areas of the pipe in contact with the support were grit blasted to get a good surface cleanliness and roughness (Rz > 60µm) before composite wrapping.
2. PIPE COMPOSITE WRAPPING WITH R4D. Wrapping reinforcement of the prepared surfaces were performed using Kevlar® tape and epoxy resin to reinforce the pipe. Two layers of R4D were applied before ROLLERKiT® installation on the supports.
3. SUPPORT SURFACE PREPARATION. Supports were also grit blasted to get a good surface cleanliness and roughness (Rz > 60µm) before receiving ROLLERKiT® pads. Degreasing and cleaning using acetone were then performed to ensure that the prepared surface was completely free from residue.
4. ROLLERKiT® PREPARATION. Cutting of the necessary number of pads to be installed. Eight pads were necessary to protect 8” pipeline and 12 pads for 14” pipeline. F3X8 filler was mixed and applicated on the support and on the ROLLERKiT® (fiber glass side).
5. ROLLERKiT® APPLICATION ON THE SUPPORT. ROLLERKiT® was then fixed on the support to protect the area between the pipe and the support. The pads were positioned perpendicularly to pipe axis to let the pipe slide freely.
6. REPAIR FINALIZATION AND VALIDATION. When curing time was over hardness measurements were performed to confirm the good polymerization of the filler and the pipe was laid down on the support.
RESULTS
In total, 30 supports were protected with ROLLERKiT® product (15 supports for both 8’’ and 14’’ pipelines). Both pipes can now slide freely on the supports avoiding coating degradation and potential galvanic contact. Pipes and supports are now protected from corrosion under supports.